Global Pumps Group is committed to providing high-quality surface protection solutions. Partnering with IND, we embarked on a project to address the coating needs of dozens of conveyor rollers in a manufacturing facility. Our goal was to create a durable, low-friction coating system that would enhance performance and reduce maintenance requirements.
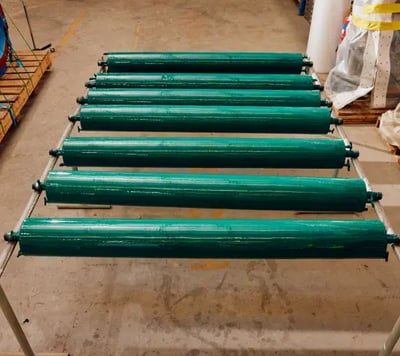
The Challenge
Our customers team faced a challenge with their roller system. These rollers are vital for their operation, but they encountered issues affecting production efficiency and overall costs.
- Constant exposure to friction, pressure, and material contact caused ongoing wear and tear, resulting in surface degradation. This degradation impacted performance, necessitating frequent replacements.
- Friction between rollers and materials significantly reduced efficiency, leading to higher energy consumption and decreased production output.
The Solution
After careful consideration, our team recommended the MetaLine coating solution. The solution comprised:
- MetaLine 900 as a primer application.
- MetaLine 795 as a spray application.
- Utilisation of MetaLine applicator.
- Testing and inspection.
Each roller underwent thorough abrasive blasting to achieve the required surface profile. A custom-built powered turning device ensured uniform application of MetaLine 795 at a consistent thickness.
Two distinctly coloured coatings layers were applied to serve as visual wear indicators: red for the base coat and green for a silicone-rich, low-friction topcoat aimed at reducing debris build-up during operation.
The Result
The application of the MetaLine coating system yielded significant results:
- Eliminated the need for lining joints, enhancing coating integrity.
- A rapid and efficient coating process, minimising manufacturing facility downtime.
- The two-tone coating system provided a clear visual indication of wear, aiding maintenance efforts.
- The silicone-rich MetaLine 795 topcoat created a smooth, low-friction surface, reducing debris build-up and enhancing operational efficiency.
- MetaLine coatings demonstrated exceptional durability, offering extended protection for the rollers and reducing long-term maintenance costs.
"We, at IND, take great pride in our expertise as industrial maintenance contractors, specialising in protective coatings. Our alliance with Global Pumps for the roller project using MetaLine has resulted in a proven success. Together, we've secured long-lasting coating solutions with our trained staff, ensuring the prolonged durability of assets."
- Oliver Kirk, Commercial Manager
Are you facing similar challenges with surface protection in your facility? Contact us today to explore how MetaLine coating solutions can optimise your operations and improve performance while reducing maintenance requirements.