Did you know that you could be killing the hose in your peristaltic pump without even knowing? We have highlighted 10 possible causes for killing your hose and how to avoid these issues to ensure you replace fewer hoses and reduce your maintenance costs and downtime.
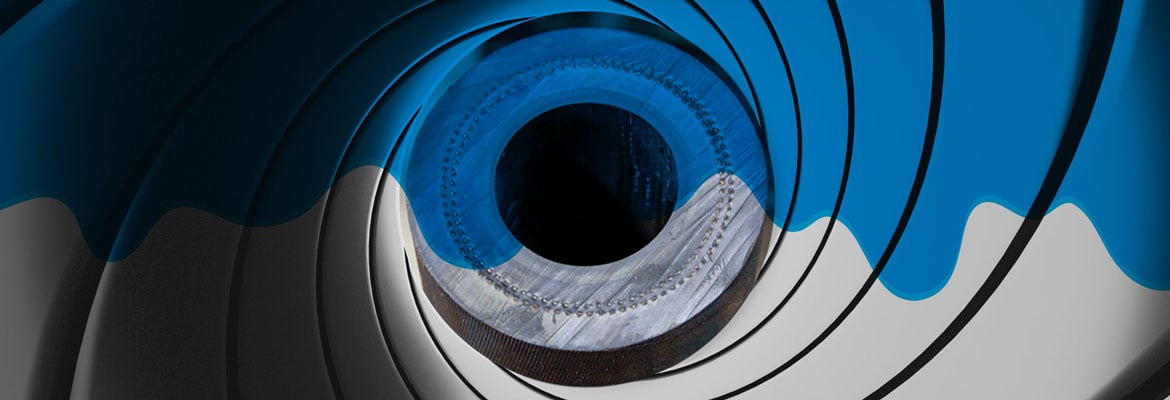
Peristaltic hose pumps are ideal for liquids and slurries with a high amount of particulate matter (up to 80%), or viscous fluids. These pumps are positive displacement pumps, with a flexible hose fitted within the casing. Peristaltic pumps have many features including accurate and repeatable dosing, energy efficiency, low maintenance and operate without manual intervention. Although, without proper hoses, there is a higher chance of pump failure.
So, what causes hoses to fail?
- Incorrect shim placement: Shim adjustment is crucial for the hose to ensure its properly squeezed for efficient operation. The shims must be set to just close the hose together without heavy compression. This can be checked with a pressure gauge.
- Flow rate: Flow rate is limited to the internal dimensions of the hose. The faster you run the pump, the higher the flow rate, but this also increases the wear on the hose causing it to fail much sooner.
- Hose/product compatibility: If the hose is pumping non-compatible chemicals or liquids, the hose will fail at a greater rate.
- Lubrication: Incorrect lubrication will create friction inside the hose and reduce hose life.
- Temperature: Ensure the maximum temperature for your pump head does not exceed the recommended max temperature.
- Pulsation dampening: If pressure surges or pulsations within the pump are not addressed, fatigue failure can occur.
- Discharge conditions: If the discharge is too long or has too many bends, it increases the friction losses. This can be avoided by having as direct route to the end point as possible.
- Not using original spare part: Using non-compatible spare parts can lead to hose pump failure. It is important to stock up on spare parts that meet the correct requirements from the correct supplier. (Yes, we stock spares!)
- Pipeline design:
- Keep the piping as straight and direct as possible. Unnecessary bends and valves cause undue stress on the entire pump.
- Utilise pulsation dampeners where possible to reduce shock loads.
- Suction conditions
- Long suction lengths rapidly wear out the hose.
- Undersized suction pipework drastically fatigues the hose. Rule of thumb, try to go 1.5 times larger than your pump flanges for your suction. I.e. 50mm pump use a 75mm suction pipe.
Global Pumps YouTube channel: What Makes Hose Pumps DIFFERENT From Tube Pumps
Maintaining your pump and identifying any issues will ensure you have a more efficient pumping process. As experts in our field, the team at Global Pumps are well placed to help solve your pumping issues and keep you running with your current equipment as long as possible. We are committed to solving the tough challenges and finding the solution to your problems.
Our team of experts are available to assist you, get in touch with us, and let us help you with your application.